在球墨鑄鐵件生產(chǎn)中,常見的鑄件缺陷除有灰鑄鐵件的一般缺陷外,還有球化不良、球化衰退、夾渣、縮松、石墨漂浮、皮下氣孔等。通常,產(chǎn)生這些缺陷的原因不單是球化處理問題,有時還有造型制芯、熔煉澆注、配砂質(zhì)量、落砂清理等許多生產(chǎn)工序的問題,因此必須具體分析。以便采取相應(yīng)的合理措施加以解決。
(1)球化不良
在鑄件或試棒斷面上分布有明顯可見的小黑點,愈往中心愈密。金相組織中.有聚集分布的厚片狀石墨1.盡量選用低硫的焦炭和新生鐵。若原鐵液含硫量過高,應(yīng)采用爐內(nèi)、爐外脫硫或相應(yīng)提高球化劑的加入量。交界鐵液一定要分離干凈,灰鑄鐵的鐵掖不應(yīng)混入球墨鑄鐵中。球化處理時,防止?fàn)t渣出到澆包中3.熔制配比適當(dāng)、成分穩(wěn)定的中間合金,并采用合適的處理溫度,注意球化處理操作。防止鐵液與合金作用過分激烈或“結(jié)死”在包底4鎂球墨鑄鐵中。加人少量的稀土,可中和反球化元素的干擾
鐵液的殘余鎂量和殘余稀土量隨著時間的延長會逐漸減少,過了一定時間后。球化劑殘余量已減少到不足以保證鑄件球化時,就造成球化衰退1. 在鐵液表面的MgS、CeS與空氣中氧作用,發(fā)生下列反應(yīng):煙狀的MgO和CeO在空氣中逸損,S返回鐵液與Mg、Ce作用又生成MgS、CeS,這樣循環(huán),Mg、Ce不斷損失2.鎂在鐵液中溶解度極小,大部分鎂以微小的氣泡懸浮在鐵液中。當(dāng)有攪拌、回包、澆注、機械振動等情況時,鎂氣泡會集聚上浮,并穿出鐵液表面。遇空氣燃澆而損失3.鎂、稀土與氧有極大的親和力。鐵液表面的鎂和稀土要逐漸氧化、鎂還有蒸發(fā)損失等1.經(jīng)球化處理的鐵液應(yīng)有足夠的球化劑殘余量5.在鐵液表面加覆蓋熔劑,如石墨粉、木炭粉、冰晶石粉等
在鑄件斷面上呈現(xiàn)暗黑色,沒有光澤,主要由琉化鎂、硫化錳、氧化鎂、二氧化硅、氧化鐵、氫化鎂等所組成,是一種非金屬夾雜物,可用硫印、氧印等方法顯示出來。一般分布在鑄件澆注位置的上表面,砂芯的下表面和鑄件的死角處1.降低原鐵液硫含量;在保證鐵液球化的前提下降低鐵液的殘余鎂量2.提高澆注溫度。若澳注沮度超過1300℃時,夾渣缺陷基本上能消除3.加入適最的稀土,以保證一定的殘余稀土量(一般為ωRE0.02%~0.04%,大件控制在下限,小件控制在上限)4.扒渣前,在鐵液表面加冰晶石粉,能使渣子流動性提高,便于將渣子扒除;扒渣后,在鐵液表面加冰晶石粉,可保護鐵液表面不再被氧化。但吸潮后的冰晶石粉遇高溫鐵液時會析出HF氣體,朝激咽喉,惡化了勞動條件。為此,在一般情況下,盡量不要使用冰晶石粉。使用時,**經(jīng)過200~250℃的烘烤5.澆注系統(tǒng)應(yīng)保證鐵液平稱注人型腔在鑄件內(nèi)部有許多分散小縮孔,其表面粗糙,水壓試臉時滲水一般認為是由于球經(jīng)鑄鐵凝固特性所決定的。其形響因素有:1.適當(dāng)提高鐵液碳、硅含量(以不產(chǎn)生石墨漂浮為度);盡量降低磷含量。鐵液球化處理后,應(yīng)進行充分孕育,保證石墨充分析出。提高自身補縮能力2.在保證球化的前提下,適當(dāng)減少殘余鎂量。保證適當(dāng)?shù)南∩蠚堄嗔?/span>(一般為ωRE0.02%~0.04%)3.合理布置澆、冒口和冷鐵,適當(dāng)提高澆注溫度,從而提高冒口的補縮能力4 提高鑄型緊實度,防止鑄件外形脹大,有利于鐵液石墨化膨脹時,得到自身補縮5.改進鑄件結(jié)構(gòu).減少鑄件壁厚的不均勻度
一般產(chǎn)生在鑄件冷卻位置的上表面,砂芯的下表面和鑄件的死角處,厚大鑄件易出現(xiàn)這種塊陷。在斷口上表面往往呈現(xiàn)均勻的一層密集的黑斑。石墨漂浮區(qū)的金相組織是球狀石里或開花石墨聚集,嚴重時石墨完全爆裂 鐵液碳當(dāng)量超過共晶點,初生的球狀石墨在高溫液態(tài)中析出,由于密度的差別和鎂蒸氣泡上浮時的帶動,使部分石墨球上浮至鑄件上表面集聚,隨后在共晶轉(zhuǎn)變時迅速長大,形成石墨漂浮。因此,碳當(dāng)量愈高、鑄件愈厚大、鐵液殘余鎂量愈低、澆注溫度愈高等,愈容易產(chǎn)生石墨漂浮1.嚴格控制鐵液的碳當(dāng),當(dāng)壁厚大于70mm的鑄件,其碳當(dāng)量必須小于4.55%,當(dāng)壁厚小30mm,碳當(dāng)量必須小于4.70%,其余按這個范圍適當(dāng)調(diào)整2.在璧厚處設(shè)置冷鐵,加快冷卻速度。減少石墨漂浮3.對于大斷面鑄件可加入少量鉬鐵或鉻鐵等強烈阻止石墨化的元素,以減少石墨漂浮4.對于壁厚相差懸殊的鑄件,可采用放大加工余或大冒口的辦法,讓石墨漂浮,在加工時被切除
經(jīng)常出現(xiàn)在鑄件上表面的表皮層下0.5~2mm處,形成直徑在1~3mm左右的孔洞,熱處理或拋丸清理后,可以清晰地發(fā)現(xiàn)這種缺陷5.硅鐵和稀土一般在低溫時要吸收氫氣,而當(dāng)它們被加入鐵液時,在高溫下,會放出氫氣進人鐵液6.從鐵液中逸出的鎂蒸氣和鐵液表面的硫化鎂與鑄型中水蒸氣發(fā)生下列反應(yīng)生成的氫、氧化銳和硫化氫氣體有可能通過鑄件表面擠入鑄件中1.在保證球化的前提下,適當(dāng)減少殘余鎂量,并盡量降低原鐵液硫含量2.提高澆注溫度,小件一般要求在1280℃以上;澆注前應(yīng)扒凈渣子3.澆注系統(tǒng)應(yīng)保證鐵液平穩(wěn)注入型腔4.嚴格控制型砂水分(一般控制在ωH2O4.5~5.5%)5.爐料盡量干凈、無銹。中間合金和孕育用硅鐵**預(yù)熱供烤,減少稀土和硅鐵帶入的氣體量6.在鑄型表面噴涂錠子油等碳質(zhì)材料,使鐵液與鑄型界面上造成還原性氣氛、在鐵液表面或鑄型表面撒上少量冰晶石粉或氟硅酸鈉等都能減少或消除皮下氣孔
顯微組織為少量大石墨球周圍共晶團邊界處均勻分布碎塊狀石墨和鐵素體。石墨球也生長連接成分枝石墨,其宏觀斷面為界限分明的暗灰色斑點,主要產(chǎn)生于大斷面鑄件熱節(jié)部位或冒口頸下主要是鑄件冷卻緩慢共晶凝固時間過長而引起的成分偏析和孕育衰退或Ce及其他活性元素過多l.應(yīng)選用純凈爐料并根據(jù)干擾元索含量嚴格限制稀土(特別是Ce)的含量(質(zhì)量分數(shù)),一般應(yīng)限制有效的輕稀土殘留量≤0.006%,重稀土殘留量≤0.018%2.控制較低的碳當(dāng)量(特別是Si<2.5%~2.6%可減少此缺陷)3.在鐵液中添加微量ωSb(0.002%~0.007%)可減少或消除碎塊狀石墨4.采用釔基重稀土鎂球化劑時可加入ωSb0.01%或ωBi0.01%,可減少此缺陷,但對沖擊性能有不良影響5.采用鋇硅鐵長效孕育劑或瞬時、型內(nèi)孕育工藝也有一定效果6.加快冷卻,例如采用帶冷卻管并通入冷卻劑不斷導(dǎo)出熱量的鑄造工藝是防止此缺陷的有力措施
出現(xiàn)于鑄件熱節(jié)中心。宏觀斷面為界限清晰的白亮塊,與該都位外觀輪廓呈相似性,但有時界限不清,常伴隨縮松。金相觀察為過冷密集細針狀滲碳體,常鄰接顯微縮松。反白口多出現(xiàn)于小件,厚大鑄件剛表現(xiàn)于熱節(jié)中心珠光體量增加或呈網(wǎng)狀滲碳體最后凝固的熱節(jié)中心偏析富集鎂、稀土、錳、鉻等白口化元素,石最化元素硅因反偏析而貧乏,增大該區(qū)殘余鐵液過冷度;同時由于孕育不足或孕育衰退不利于石墨形核;薄壁小件熱節(jié)比大件冷卻速度快,因此在偏析過冷和孕育不足的熱節(jié)中心形成細針狀滲碳體和縮松。鐵液中含Cr 、Te或稀土殘留量過高易出現(xiàn)此缺陷1.在保證球化條件下盡量減少殘留鎂和稀土量。必要時使用低稀土球化劑2.防止?fàn)t料內(nèi)混入鉻等強烈白口化元素3.強化孕育,如采用后期孕育工藝或用鋇硅鐵長效孕育劑轉(zhuǎn)自: 熱加工行業(yè)論壇
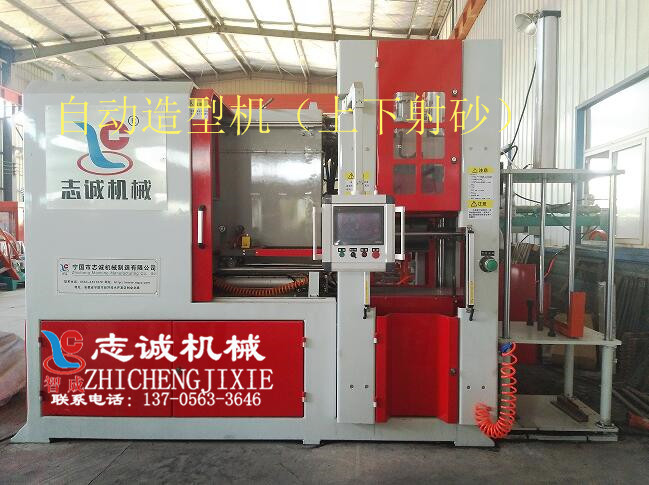
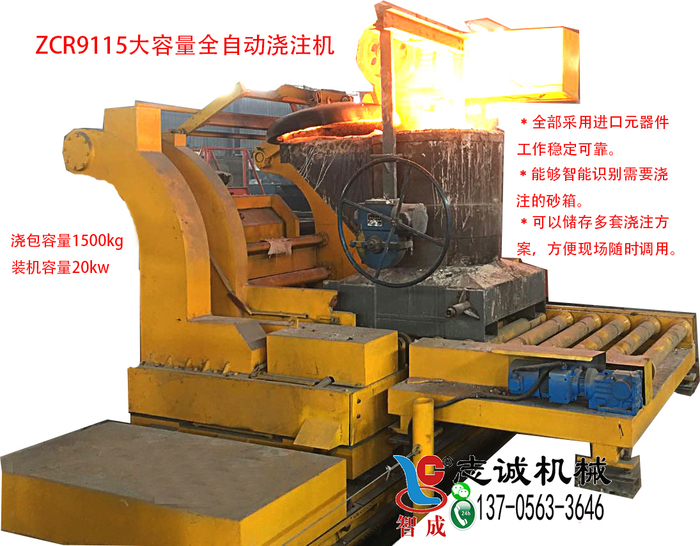
上一篇:如何讓球磨機發(fā)揮**優(yōu)勢
下一篇:減少鑄件缺陷的10大準則